Why use Lifepo4 battery packs?
Lifepo4 Battery cells are like eggs. Cells come in fixed voltages and capacities. If you need more voltage, you can deal with multiples of the cell voltage. You can’t get half an egg, and you can’t get half a cell, at least in voltage. Cell capacities do vary, particularly with a supplier like PowerStream that has a great variety of cell sizes available, but voltages don’t. All NiCad or NiMH cells are 1.2 volts nominal, lead acid is 2.0 volts nominal and the various lithium technologies are about 3.6 volts per cell. If you need more voltage you have to add them in series, if you need less voltage you need some kind of voltage regulator or DC/DC converter.
If you need more current than a single cell can supply you may need to put cells in parallel. If you need more capacity to give longer run time you may also put cells in parallel.
Many times the physical configuration makes it more attractive to use many small cells rather than a few large cells, since a large block is harder to fit than several small subunits.
Geometry and Topology Considerations for Assembling Lifepo4 Battery
There are an infinite variety of battery pack combinations. Here are the most popular:
Case 1: Ladder, linear, F type, or radial
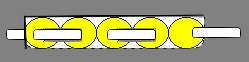
Note that the straps will both come off the top when there are an even number of cells, and one off the top, the other off the bottom when there is an odd number of cells. With a connector and heat shrink wrap they look like this:
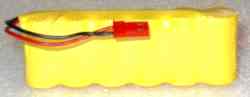
The size of a ladder pack is D x nD x H where D is the diameter of the cell, n is the number of cells, and H is the height of the cells.
Case 2: Multi-row cells Lifepo4 battery
There are two ways to start packing them. One could be called the cubic, and the other face centered cubic, or nested.
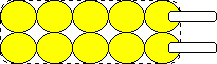
Cubic packing is in neat rows. The size of such a pack is nD x mD x H, where n is the number of cells in a row, m is the number of rows, D is the cell diameter, and H is the cell height.
Case 3: Face centered “cubic”
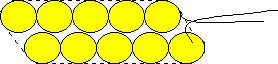
Face centered cubic packing is nested to take up less room. Calculating the size takes a little geometry, which follows:
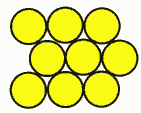
The size is L x W x H where
L = (n +½)D
W = [0.866(p-1)+1] D
H=H
p is the number of rows wide.
Case 4: FCC with alternating long and short rows
If there are alternating long and short rows, such as the 3,4,3 ten cell pack, the formulas are

L = mD
W = [0.866(p-1)+1] D
H = H
Where m is the number of cells in the longest layer, and p is the number of layers. With heat shrink it looks like this:
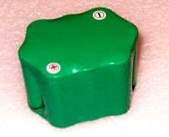
Case 5: Fixed channel width optimization
What if you have a fixed width channel and want to stagger the cells to maximize the number of cells per unit width? Pull out your high school geometry book, this is trickier!
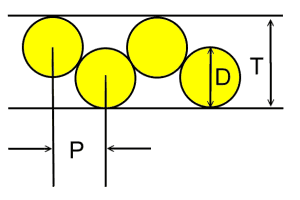
The distance P between the cells of Diameter D in a channel with height T is P = sqrt (2TD-T^2)
So if you have 18mm diameter batteries fitting into a 25.4mm channel, the distance between the cells is 16.8mm. In this case you can fit in an extra cell for every 15 cells, or save 1.2 mm of width per cell.
Case 6: Packing cells in a tube, 3 cells.
For a 3 cell pack, you can put the cells in a tube
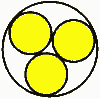
The diameter of the outer circle is 2.16 D.
Case 7: Packing cells in a tube, 4 cells.
For a four cell pack in a circular tube
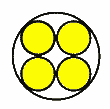
The diameter of the circumscribing circle is 2.41 D.
For example, with AA cells the diameter is 14.2 mm, so three would fit into a tube 30.7 mm in diameter, and four would fit in a tube 34.22 mm in diameter. Of course you will want to expand this slightly to account for up to 0.5 mm variation in cell diameters.
Case 8: Packing cells in a tube, up to 91 cells
Cylindrical batteries in a tube of diameter “D” | Approximate diameter of the circumscribing circle | Scheme |
2 Cells | 2D | Side by side |
3 Cells | 2.16D | Triangle |
4 Cells | 2.414 D | Square |
5 Cells | 2.70 | Pentagon |
5 Cells | 3D | Square with one inside |
6 Cells | 3D | Hexagon |
7 Cells | 3D | Hexagon with one inside |
8 Cells | 3.305D | Heptagon with one inside |
9 Cells | 3.62D | Octagon with one inside |
10 Cells | 4.4D | Pentagon with 5 more cells symmetrically arranged around he outside |
10 Cells | 3.92D | Nonagon with one inside |
11 Cells | 4D | Nonagon with two inside |
12 Cells | 4D | Nonagon with three inside |
13 Cells | 4.24D | Decagon with three inside |
14 Cells | 4.4D | Decagon with four inside |
15 Cells | 4.55D | Undecagon with four inside |
16 Cells | 4.9D | Dodecagon with four inside |
19 Cells | 5D | Hexagonal close packed |
37 Cells | 7D | Hexagonal close packed |
61 cells | 9D | Hexagonal close packed |
91 Cells | 11D | Hexagonal close packed |
Case 9: Linear, or L-type, or Axial
This is a stack of cells end to end.
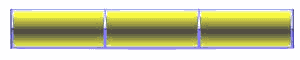
These packs are usually constructed by standing two cells side-by-side, and welding a nickel strip across the terminals, as in the ladder pack. The cells are then bent end to end by bending the nickel connecting strip in a “U” shape. Allow a thickness increase of ½ to 1 mm per junction for this.
Thermistor
Please do not invent your own temperature control system. The industry standard thermistor is NTC 10K at 25°C and B=3950.
Lifepo4 battery Pack assembly
Solder versus Weld
Most battery packs are spot welded together using nickel strip for contacts. Soldering directly to the cells is dangerous for the cells. It is easy to melt or disturb the safety vent, thwack the seals, or cause internal shorting if the heat is too high. This damage might not be noticeable until later.
However, not everyone has a capacitive discharge spot welder, so PowerStream has instituted a program where we can spot weld nickel solder tabs at the factory. This is cheap, and allows the end user to solder together custom packs easily without fear of damaging the battery.
Heat Shrink Tubing
The most common way to hold the pack together is to use heat-shrink tubing. This has sufficient strength for small packs, but as the weight increases more structural strength is necessary. This is done by adding a sheet of structural material, usually plastic or fish paper, to the top and the bottom of the pack. If the battery is to be put into another structure, either a plastic case, or the system box, it is still important to tie it together with heat shrink or tape for ease of handling.
When building and using battery packs be careful not to inadvertently short the cells. A pack of cells wired in series will become shorted if the cases of adjacent batteries touch, since the outer case is a terminal. This can happen if the cells are shrink wrapped, film wrapped or painted and the batteries rub against each other. Brittle shrink wrap is known to shred under stress, leaving the bare cell walls to touch. If there is danger of this happening cardboard sleeves are used instead of just the heat-shrink tubing.
Another source of strength is the use of glue where the cells touch. Cyanoacrylates are sometimes used to tack things together, but can weaken the vinyl heat-shrink if not reinforced. A hot-melt glue is more forgiving.
Lifepo4 Battery Holders
When using or designing battery holders make sure there is adequate provision for short cells, long cells, or wide cells. Keep sharp clip edges from touching the cell where they could cut the film or paint, causing a short between cells held by the same clip.
Potting Lifepo4 battery?
Batteries expand and contract during charge and discharge. Potting a battery is not a good idea, unless there is some provision made for this dimension change. This can be compensated for by including a foam pad to absorb the stress of expansion. There is also a problem with venting unless the potting is such that the seals are not covered. You don’t want the pressure to build up to the point it blows the potting material apart.
Cases and Cabinets?
Over the course of life most batteries release hydrogen, and sometimes oxygen. Take this into account if you are designing a closed system, such as waterproof lights, weatherproof installations, etc. Some method of releasing or absorbing the hydrogen, flooding with air or inert gas should be used. In closed cabinets some provision for ventilation is necessary to prevent hydrogen gas from accumulating.
Electrical and System Considerations
How many amp-hours do I need?
Cell capacity is rated in amp-hours or milliamp hours. The symbol for capacity is C. This is amps times hours. Divide by hours and you get amps, divide by amps and you get hours. For example a 5 amp hour battery is the same as a 5000 milliamp-hour battery. If you want to discharge in 10 hours, you can get a current of 5/10 = 0.5 amps. If you need 100 milliamps current, then you can run for 5000/100 = 50 hours.
Often a discharge or charge rate is given proportional to C. So a discharge rate of C/5 means C/(5 hours), or the constant current to fully discharge the battery in 5 hours.
The calculation of run time versus current is a rough estimate, but is accurate under the right conditions. The faster you discharge, the lower the capacity of a battery. This trade-off depends on the battery chemistry and construction. Usually the capacity of a battery is quoted at a C/20 discharge rate. So an 12 amp hour battery sealed lead acid battery will actually put out a steady 0.6 amps for 20 hours. However, if you discharge the same battery at 12 amps, you would expect to run an hour, but you will only last for 22 minutes. Also, if you wan to run at 10 milliampere you will get less than the expected 1200 days, since self-discharge of the battery will limit your run time.
Different battery chemistries differ in this respect. Lead acid batteries are probably the worst at the rapid discharge end of the scale. NiCads and NiMH are much better.
How do you determine the current that your system draws?
The best way is to measure with a current meter and an adjustable power supply (usually the current meter is built into the power supply). Set the power supply to the highest voltage that the system is rated at and measure the current, then set the power supply to the lowest voltage that the system is rated at and record that current. Adding a measurement half way between the two will give you an idea of where the lowest power consumption point is (power is voltage times current). The idea is that you want to design your pack so that the voltage swing of the batteries (see below) is adequate, and where the power consumption is the least. Some systems will show approximately constant power consumption no matter what the battery voltage is, and some will have a sweet spot where the power is lowest.
If a variable power supply is not available, chart the current versus the voltage of the battery during a discharge cycle.
If making actual measurements is not possible, use the system data sheet, or the “boilerplate” sticker on the back to find the rated wattage or input current. This will usually give you a high estimate, or a peak value.
Lifepo4 Batteries in Series and Parallel.
With NiCad and NiMH cells are best used in series, not in parallel. This is because keeping the battery pack equally yoked during repeated charge and discharge conditions can be a problem. So a good approach is to choose the cells that will give you the capacity and current that you need and put them in series to get the voltage you need.
With lead acid and lithium batteries parallel and even series + parallel packs are common.
Series
When used in series, the voltage is multiplied but the amp-hours stays the same. So three 5AH 3.6V in series would give a 5AH 10.8V pack.
Parallel
When used in parallel the voltage stays the same and the amp-hours multiply. So three 5AH 3.6V cells in parallel would give a pack that is 15AH and 3.6V.
The first question to answer is “how much voltage do I need?” The second is “how many cells in series do I need?”
The voltage of any cell is a moving target. When fully charged the voltage will be higher than nominal, and at the end of capacity the voltage will be lower than nominal. The following table shows the range of the various chemistries:
Chemistry | Type | Nominal Voltage |
Fully charged voltage |
Fully discharged voltage |
Minimum charge voltage |
Lithium Ion Lithium Polymer |
Secondary | 3.6V | 4.2V | 2.8-3.0V depending on the protection circuit board cut off | See this web page for the trade-off between capacity and charge voltage |
Lithium iron phosphate | Secondary | 3.2V | 3.65V | 2.8-3.0V depending on the protection circuit board cut off | See this web page for the trade off between capacity and charge voltage for lithium iron phosphate batteries |
NiMH | Secondary | 1.2 V | 1.4 V | 1.0 V | 1.55 V |
NiCad | Secondary | 1.2 V | 1.4 V | 1.0 V | 1.50 V |
Lead Acid | Secondary | 2.0 V | 2.1 V | 1.75 V | 2.3 – 2.35 V |
So a 10 cell pack of NiMH cells would have 14 Volts when fully charged, and run down to 10 volts when fully discharged. Your system must be able to tolerate this voltage range.
Furthermore, if you want to be able to charge while your system is running, the system must be able to accept the charging voltage, which is always higher than the nominal or the fully charged voltage. Work with the charger manufacturer to make sure that you have this problem solved.
Matching Cells in a Pack
Be careful to match the cells in a battery pack. When a battery pack is near zero volts under load the weaker cells will go into reversal, and suffer damage and perhaps venting.
Resistance of the Nickel Strip in Lifepo4 Battery Assembly
Nickel foil is used to spot weld packs together. Nickel is fairly low resistance, yet has enough resistivity to be spot welded. It is strong, has very good corrosion resistance, and will not oxidize easily.
The resistivity of nickel is 6.9 x 10-6Ohm-cm. The formula to be used to calculate the resistance for a nickel strip is R = { L / ( w*t } rho, where L is the length of the strip, w is the width, and t is the thickness, all in cm. The length L can be estimated as the diameter of the cells. The following table gives typical values. This is a conservative estimate, since in many cases the spot welds are closer to the edge of the than we have assumed.
Cell Size | Foil Thickness | Strip Width | Strip length | Resistance |
AA | 0.018cm | 0.5cm | 1.4 cm | 1.0milliOhms |
AA | 0.025 | 0.5 | 1.4 | 0.76 |
Sub C | 0.025 | 0.5 | 2.3 | 1.2 |
Sub C | 0.025 | 1.0 | 2.3 | 0.6 |
Sub C | 0.018 | 0.5 | 2.3 | 1.7 |
D | 0.018 | 1.0 | 3.3 | 1.2 |
D | 0.025 | 1.0 | 3.3 | 0.9 |
D | 0.025 | 2.0 | 3.3 | 0.4 |
This table gives examples of the calculation of the resistance of nickel spot weld strips.
LifePO4 Batteries Related Products:
Related Products Application:
LifePO4 Batteries Related Posts:
Tag in this article: #LiFePO4 Battery
Tips: more detail information, for deep cycle LiFePO4 battery。